

The head designer generally has access to all of the assembly models and is responsible for merging them together into the final machine design. Often, several different design engineers may be working concurrently on a machine or product that has multiple assembly parts. Each of these components with the complete assembly is represented as solid models.
#ASSEMBLY 4 CAD SOFTWARE#
These types of sophisticated software systems are designed to handle multiple files that represent the individual components that make up an entire product or machine. Each component within an assembly is represented as surface models.Īssembly modeling in CAD refers to both the technology and the techniques used by 3D CAD through which the design intent of a part or assembly is accurately and unambiguously described by a 3D virtual model. What is Assembly Modeling?Īssembly modeling is a technology and process of using CAD (computer-aided design) and product visualization software to design components of a product. In fact, entire college courses can be devoted to various projects that are designed to develop 3D design skills and knowledge.
#ASSEMBLY 4 CAD HOW TO#
Learning how to carry out complex operations within a 3D program in order to create a “working” assembly model can take time. Using a 3D so ftware program, such as CATIA, various 3D parts can be combined into complete assembly models by rotating the parts, sliding them, exploring various ways to join them and employing other design concepts that are far beyond the geometric representations of the 2D CAD. README.Traditional 2D drafting is capable of showing the geometry of simple 3D parts, however solid models extend that ability by being able to merge complex assemblies of parts into a complete mechanism. See also this excellent tutorial by Zolko. Sketches are less susceptible but not fool proof especially if the motion is over a large range. You may be able to attach to a body edge and align the LCS so that it will follow your motion but also be aware that it will be susceptible to the TPM problem if you modify any of the features. If you cannot describe the motion mathematically in Expressions then your next best option is to use the Sketcher constraints and solver. It locks all degrees of freedom when you attach one LCS to another which can only be freed with Attachment Offset displacements or rotations and/or Expressions. Remember that Assembly4 does not have an explicit assembly motion solver. Without knowing what your exact configuration comprises, it may be that you do not need a sketch to solve for the positions as your animation variable changes. Just a confirmation, to make a sketch is not mandatory, it's just to check. If you have a solution or at least an indication on what could explain this behaviour, it will be an help for me. What could happen? do I need to "block" the slider on the arm and to relax it after ( because of course, I want to move the slider when I've reached the good angle in the first movement.) and if yes, how to block? But probably, my issue is maybe due to the relative positionning of the LCS which could be perturbated by the rotation.
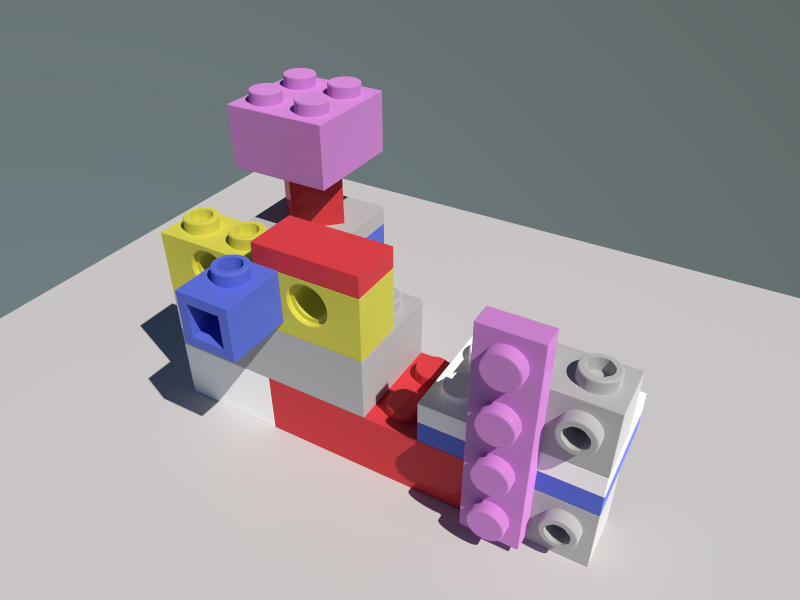
but I was excpecting the second relationship ( the slider relationship) not to move And it does'nt work this way when changoing the angle of the rotation, the positionment of the slider does"t stay on the arm. I've tried to change the value of angle in the connection and it's working fine. I've placed LCS on each part, and I've "made" the connection between regarding LCS on both parts and that"s working fine in a static way.īut my concern is when I try to animate all that. 1) One body blocked this body has an axle Z is the rotation axisĢ) One arm which a hole this hole is centered on the body's axis allowing only a rotation between the arm and the body, this arm has also a prismatic section in order to guide a sliderģ) One slider with the same prismatic section as the arm
